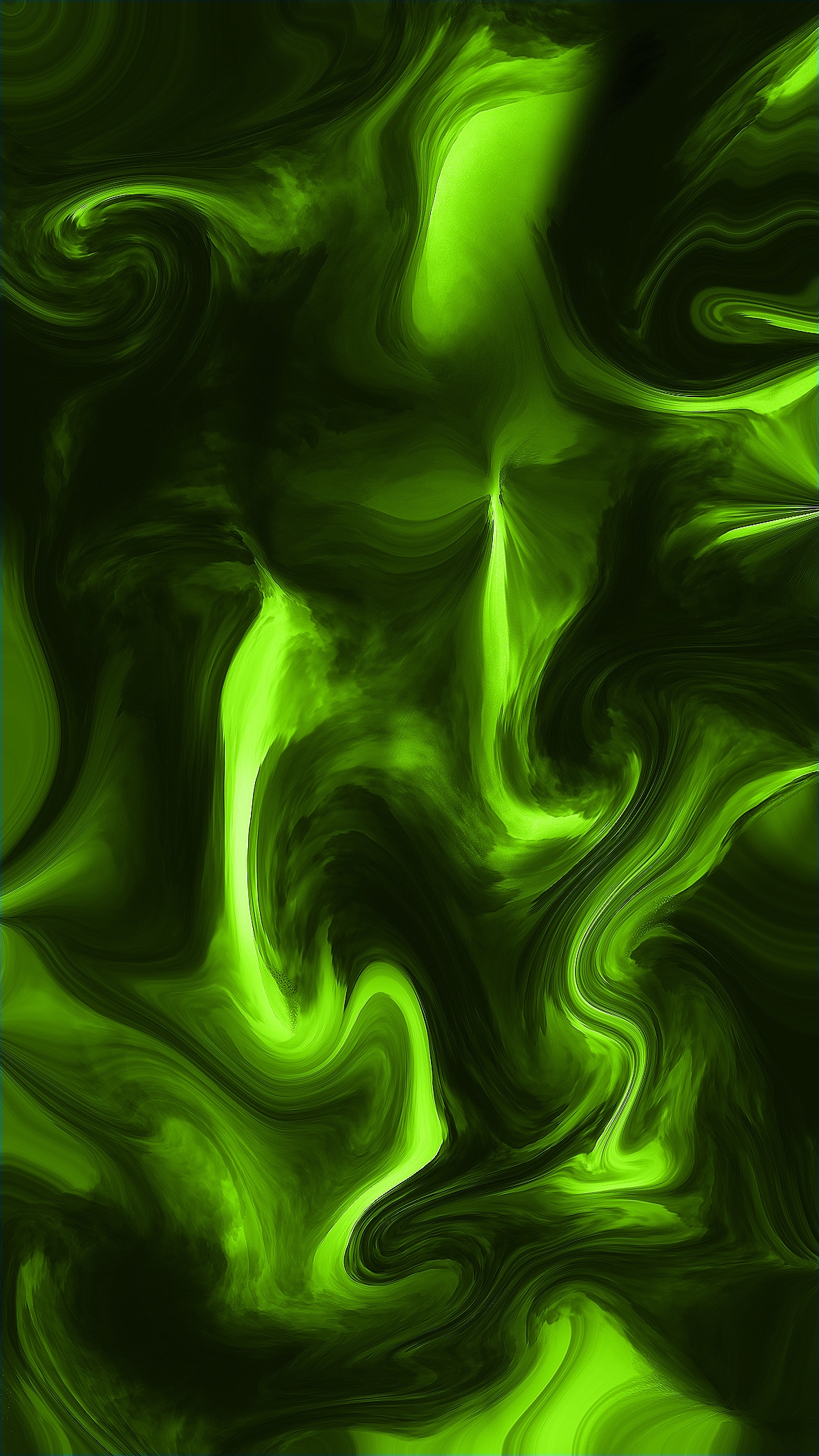
Operations Planning
IMPORTANT ELEMENTS OF OPERATIONS PLANNING
- reducing wastages
- producing the range of product that are forecast to be demanded
- employ and keep an appropriate number of staff
- keep sufficient inventory
OPERATIONS DECISIONS
- Decisions taken by operations manager can have a significant impact on the success of business. These decisions are often influenced by marketing factors, availability of resources and technology.
- Marketing Factors- there is a link between operations department and marketing department. Operations manager requires information pertaining to estimated market demand when planning future production levels. Thus, the operations manager will try to match supply to potential demand
- The availability of Resources- the production department use resources to produce goods and services. These resources include land, labour, capital equipment and raw materials. Thus, the availability of raw materials or lack of them can influence a number of important operations decisions. The business must decide on the best location and nature of the production method
- Technology- the provision of services and also the manufacturing of goods has changed. Firms now use digital technology and there two main forms of Computer Aided Design (CAD) and Computer Aided Manufacturing (CAM)
- COMPUTER-AIDED DESIGN (CAD)
- Involves the use of computer programs to create 2 or 3 dimensional graphical representations of physical objects. It is most used in architectural designs and on computer animations. It can provide special effects on movies and advertising.
- CAD is also used in furniture manufacturing and the software is used to calculate the optimal size or shape of the product. Engineering department also uses CAD to analyse the components of various structures.
- BENEFITS OF CAD
- Lower product development costs
- Increased productivity
- Improved product quality
- Good visualisation of the final product and its constituent parts
- Errors are minimised i.e. it is more accurate
- LIMITATIONS OF CAD
- Complexity of programs
- Need for extensive employee training
- It is more expensive i.e. computer software used
- COMPUTER-AIDED MANUFACTURING (CAM)
- Involves the use of computer software to control machine tools and related machinery in the manufacturing of components or complete products. Processes in a CAM process are controlled by computers. Thus, a high degree of precision and consistency can be achieved than a machine controlled by a worker.
- BENEFITS OF CAM
- Quality products are produced
- Faster production and increased labour productivity
- CAM can be combined with CAD to produce a wide range of products
- More flexible production allowing quick changeover from one product to another
- LIMITATIONS OF CAM
- High costs of hardware, programs, and employee training
- Hardware failure can be time-consuming to solve
- Computer system can be easily affected by virus
- Small firms cannot afford it
- COMPUTER-AIDED DESIGN (CAD)
FLEXIBILITY AND INNOVATION IN PRODUCTION
- Operational Flexibility- refers to the ability of a business to vary both the level of production and the range of products following changes in customer demand. The level of demand is not constant, it may increase or decrease. Thus, the business must be able to respond quickly to changes in demand.
- Way to achieve operational flexibility:
- Buy more equipment
- Construct or buy new buildings
- Maintain the efficient stock levels
- Employ part-time or temporary labour force
- Way to achieve operational flexibility:
- Process Innovation- refers to the use of a new or much improved production method or service delivery method
- Elements of process innovation
- Use of robots in manufacturing
- Faster machines to manufacture microchips for computers
- Use of bar codes and scanner for tracking inventory
- Use of internet to track the exact location of parcels being delivered worldwide and improve the speed of delivery
- Benefits of process innovation
- Being able to get more accurate and reliable information on the performance of various departments
- Being able to save time i.e. less paperwork is involved
- Increased professionalism and image to suppliers and customers
- Increased productivity
- Reduction of costs in the long run i.e. in the short-run the costs of acquisition are high
- Cheaper production methods makes the business more competitive
- Elements of process innovation
PRODUCTION METHODS (OPERATION METHODS)
Each firm must carry out production designing. Production design refers to the scheduling of production which involves organising the activities in a manufacturing plant or service industry to ensure that the product or service is completed at the expected time. There are four basic ways of production design namely job, batch, flow production, and mass customisation.
- The chosen production method depends on:
- Nature of product- unique products require jobbing, group of identical products require batch and identical products requires flow production
- Size of business- small businesses use jobbing and batch while large firms use flow. This is because flow production is expensive to set up.
- Size and location of the market- the firm must take into cognizance the volume of output required. If the demand is high but not in large quantities, batch is used. Mass marketing requires flow production.
- Demand of the product- less frequent demand requires jobbing while larger and fairly steady demand requires flow production.
JOB PRODUCTION
- Used when a single product or small orders are completed by one/ a group of people from start to finish to meet the customer’s individual requirements. Thus, the products are customised (produced according to the customer’s specifications)
- Each order is different, and it may not be repeated at all. It is usually used by small and new firms to make products like wedding cakes, wedding gowns, building plan etc
- It is the most expensive form of production, very labour intensive (requires few machines) and requires highly multi-skilled labour.
ADVANTAGES
- Product can be tailored to meet customer needs
- It is suitable for personal services e.g hair cuts
- The workforce has greater involvement with the product. This increase job satisfaction.
- The product meets the exact requirements of the customer. This result in guaranteed customer satisfaction.
- Use of skilled staff results in the production of quality products
- High employee motivation. This is because there is no monotony since each task is different from others
DISADVANTAGES
- Need a highly skilled workforce, competent supervisors, and management. Specialists are costly to attract and to keep at a business
- Production takes long. This is because there is no automation or use of complex machines. It is usually done manually.
- Special materials are required leading to high cost of production. Only quality material is required.
- Products are specially made to order, and any error is very expensive.
BATCH PRODUCTION
- A method of production where items are made in groups with similar characteristics. Each item in a group of products passes through a stage of production at the same time.
- It is the production of a limited number of identical products to meet customer order or specifications and each order is called a batch.
- It falls between job and flow production. It is commonly used by bakeries, furniture manufacturers, etc
ADVANTAGES
- It gives variety to workers’ jobs. This is because workers work on different batches that may require different skills- this removes boredom from work
- It allows more variety to be produced. This will increase consumer choice
- Materials can be bought in bulk. This will give bulk discounts to the business
- Unit cost is lower than Jobbing. Producing more goods reduces average cost of production
- Production can be easily changed from one product to another
DISADVANTAGES
- No product will be completed before another, lead time
- Increase in costs since there is need for a very efficient control system in planning production
- Warehouse space will be needed for stock of raw materials and components.
- Machines have to be reset between production batches. This will result in delayed production and output is lost
FLOW PRODUCTION
- It is also known as mass/ continuous/ serial or repetitive production.
- It is the production of large quantities of a product in a continuous process. The products produced are identical or standardised
- It uses a series of repetitive processes so that each item moves on to the next stage as soon as a process is completed. Products pass along a conveyor belt or assembly line
- It requires a high degree of standardisation and specialisation
- It is more capital intensive- it requires more machines, robots, and automation than people.
- Requires heavy investment because of the need to buy expensive machines and automation.
- The following products are produced using flow or mass production: chemicals, fuels, packaged food products, cars, televisions etc
ADVANTAGES
- Automation allows goods to be produced quickly
- Mass production enables the business to enjoy the economies of scale which leads to lower prices
- Automated production lines can operate 24 hours a day and 7 days a week
- Time is saved since goods move on conveyor belts
- Promotes specialisation. Repetition of the same task makes the employee more skilled
- Materials can be bought in bulk. This will give bulk discounts to the business
DISADVANTAGES
- If one machine breaks down, the whole production line will have to be halted
- It is very costly. This is because machines and automation are very expensive to buy
- Repetition of the same task can be boring to the worker
- It is not flexible. Once production lines are set it is difficult to switch to other methods
- High warehousing costs since the mass produced goods must be stored before delivery to consumers
- Use of machines puts people out of their jobs
- Only suitable for products with a large market and high demand
MASS CUSTOMISATION
- It’s a flexible mass production system enabling customers to specify what features of a product/ service they want.
- This process combines the latest technology with multi-skilled labour force to use production lines to make a range of varied products. This allows the business to move away from the mass- marketing approach with high output of identical products.
- The businesses will now use focused or differentiated marketing which allows for higher added value. Few changes to the products are made using flexible computer aided production systems to produce items to meet individual customers’ requirements at mass production cost levels
ADVANTAGES
- Accurate records are kept. This is because of the use of computers to keep records
- Greater job satisfaction as boring and routine tasks are now being done by computers
- New products are produced as new methods of production are introduced
- Better quality products are produced due to better production methods
DISADVANTAGES
- It is very expensive to set up. Computers, robots, and machines are very expensive
- Technology will become out-dated. Technology keeps on changing
- Employees may need to be retrained to use the new technology. This adds to business costs
- Increased unemployment as workers will be replaced with machines
PROBLEMS OF CHANGING OPERATIONS METHODS
- Setting up an operation method takes time, planning and capital. To change from one method to another would mean taking apart the machinery and equipment and redesigning the whole production system.
- It would also mean that it might be necessary to redesign the product. It would be extremely difficult and very expensive to produce some batch produced products by flow production
BUSINESS LOCATION
- Business have to make the important decision of the best place to locate in order to operate well. The location of the business can affect its costs, its demand, its image, and its ability to attract employees to work for it.
- Thus, location choices should not be taken lightly and will involve decisions at the most senior level. Influence on the final location depends on the type of business, size, demands of the production process and the market
- Optimal location- a business location that gives the best combination of quantitative and qualitative factors
QUANTITAVE FACTORS THAT AFFECT LOCATION DECISIONS
- Site and other capital costs such as building costs
- Labour costs- depends on whether the business is labour intensive or capital intensive
- Transport costs- for example, bulk-gaining goods would want to locate close to the market
- Sales revenue potential- certain locations can add status and image to a business which allows value to be added in the eyes of the customer
- Government grants- grants may be offered to act as an incentive
TECHNIQUES USED TO DECIDE LOCATION
- Profit estimates- by comparing the estimated revenues and costs of each location, the site with the highest annual potential profit may be identified
- Limitation- annual profit forecasts alone are of limited use- they need to be compared with the capital cost of buying and developing the site
- Investment appraisal- location decisions often involve a substantial capital investment; the payback method, can be used to estimate the location most likely to return the original investment quickest
- Limitation- these methods require estimates of costs and revenues for several years for each potential location which introduces a degree of inaccuracy
- Break-even analysis- It calculates the level of production that must be sold from each site for revenue to just equal total costs. The lower this break-even level of output, the better that site is, other things being equal.
- Limitation- break-even analysis should be used with caution and the normal limitations of this technique apply when using it to help make location decisions
QUALITATIVE FACTORS THAT INFLUENCE LOCATION DECISIONS
- Safety
- Room for further expansion
- Manager’s preferences
- Ethical considerations
- Environmental concerns
- Infrastructure
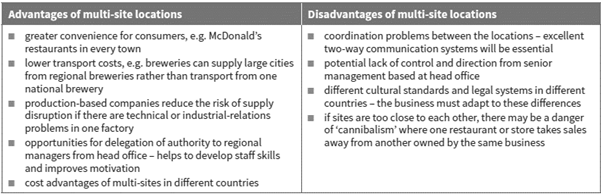
THE OPPORTUNITIES AND PROBLEMS OF ENTERING NEW MARKETS ABROAD
- Opportunities of entering new markets abroad
- Sales growth- new markets increases a firm’s sales. This may boost company sales revenue as new customers are buying the product
- Increased profits- The new markets abroad may result in more profits to the business. Increased sales volumes mean more profits to the business
- Improved business image- a good image locally and internationally may result because the business is selling in foreign and competitive markets, the business products will be seen as of high quality
- Earn foreign currency- foreign currency obtained can be used to acquire new machinery in foreign countries
- Problems of entering foreign markets
- Cultural differences- different countries have different cultures. The firm needs to understand the culture of the country they intent to enter for them to be successful.
- Lack of knowledge- the business may lack marketing knowledge of the new country or market e.g consumer preferences, goods offered by competitors, advertising methods and distribution methods
- Lack of foreign currency- the business may not have sufficient foreign currency to pay for workers, taxes, rentals, and advertising
- How to overcome such challenges
- Form joint ventures- the business can join with an existing local business. The business will have knowledge from the local business who understands the local market.
- Use local agents and local dealers- the business can engage local dealers to distribute and market the goods for business. The local agents have local marketing information, and they know the best methods to distribute the goods
- Primary and Secondary research- essential information about the products, customers, markets is obtained through conducting market research.
ECONOMIES OF SCALE
- Refers to the cost saving advantages that a business can exploit by expanding their scale of production. Thus, making things cheaper because they are bigger. The effect is to reduce the long run average cost of production over a range of output. Economies are divided into internal and external economies of scale
- INTERNAL ECONOMIES OF SCALE- internal economies of scale arises from the growth of the firm itself. Thus, the average cost will decrease as the firm employees more capital and labour
- Purchasing Economies of Scale- Large firms receive discounts when they buy raw materials in bulk. Thus, the cost of acquiring raw materials will decrease leading to a fall in the unit cost/ average cost
- Marketing Economies of Scale- A large firm can spread its advertising and marketing budget over a large output. Advertising is charged per total time on airplay (TV/ Radio) or space (Newspaper) not on the size of the business. As the firm grows in size, the average marketing cost will decrease
- Financial Economies of Scale- Large businesses may be able to access finance at lower interest rates because of the growth of the business. Large businesses are usually rated by the financial markets to be more ‘credit worth’ and have access to credit facilities with favourable rates of borrowing
- Managerial Economies of Scale- Large scale manufacturers can afford to employ skilled workers to supervise and to carry out production. Effective leadership can also lead to an improvement in worker motivation. Skilled workers will also help reduce wastages. Employees also become experts due to the length of experience in a market and the cost per unit will decrease
- Technical Economies of Scale- Large scale businesses can afford to invest in very expensive and specialist capital machinery
- Risk Bearing Economies of Scale- A large firm is able to provide a wide range of products in different markets.
- INTERNAL ECONOMIES OF SCALE- internal economies of scale arises from the growth of the firm itself. Thus, the average cost will decrease as the firm employees more capital and labour
DISECONOMIES OF SCALE
- Diseconomies of scale leads to a rise in the long run average cost. Average cost rises due to firms expanding beyond their optimum scale (Optimum-right size)
- SOURCES OF INTERNAL DISECONOMIES OF SCALE
- Managerial Diseconomies of Scale- monitoring the productivity and quality of output from thousands of employees in big corporations is imperfect and costly
- Administrative Diseconomies of Scale- these are associated with the bureaucratic structures of large firms where long channels of communication and complex administrative procedures delay effective action. Instructions from the top management may be partly or completely distorted if they are to follow a long channel of communication.
- Over-specialisation- workers in large firms my feels a sense of alienation and subsequent loss of morale. If they do not consider themselves to be an integral part of the business, their productivity may fall leading to wastage of factor inputs and higher costs
- SOURCES OF INTERNAL DISECONOMIES OF SCALE
ARE DISECONOMIES AVOIDABLE?
- Management by objectives: This will assist in avoiding coordination problems by giving each division and department agreed objectives to work towards that are components of the long-term aims of the whole business.
- Decentralisation: This gives divisions a considerable degree of autonomy and independence. They will now be operated more like smaller business units, as control will be exercised by managers ‘closer to the action’. Only really significant strategic issues might need to be communicated to the center, and such issues might be the only ones requiring decisions from the center.
- Reduce diversification: The recent movement towards less-diversified businesses that concentrate on ‘core’ activities may help to reduce coordination problems and some communication problems.